I am once again cross posting from Supertopo. I am linking to the photos on Supertopo this time to see if they will let me do that.
I managed to get a copy of an old paper that is the only one that I can get my hands on that discusses how a percussion drill does its job. "Basic Studies of Percussion Drilling" was published in January 1959 in Mining Engineering on page 68-75. In the introduction the author states that although materials and equipment have improved, rock drill bits have undergone no major modification since they were first used in the 1860's for drilling blast holes in mines. Looking at his discussion, I would say that other than developing carbide tips, not much has changed since 1959 either.
The main area of interest to me is the investigation of how the drill tip penetrates the rock and breaks it up. They figured this out with high speed photography. As the tip impacts the rock, the rock below the tip crushes into a fine powder. The tip penetrates the fine powder and the powder expands outward in its space causing chips to flake off on each side. For a given volume of rock, it takes more energy to pulverize the fine powder than a corresponding volume of chips. This means we want to minimize the powder and maximize the chips. You can minimize the powder by having a sharp drill and by having a drill tip with a small included angle. If the tip is too sharp, it dulls easily and if the included angle is too small the bit will chip. The optimum angle is probably a function of the rock and the bit material. Carbide is very brittle so it probably needs a larger angle than HSS. On the other hand, carbide is very hard so it can be kept sharper. The paper states that the angle must be 90 degrees or less to result in any chips at all. Carbide bits are very close to 90 degrees so not very efficient.
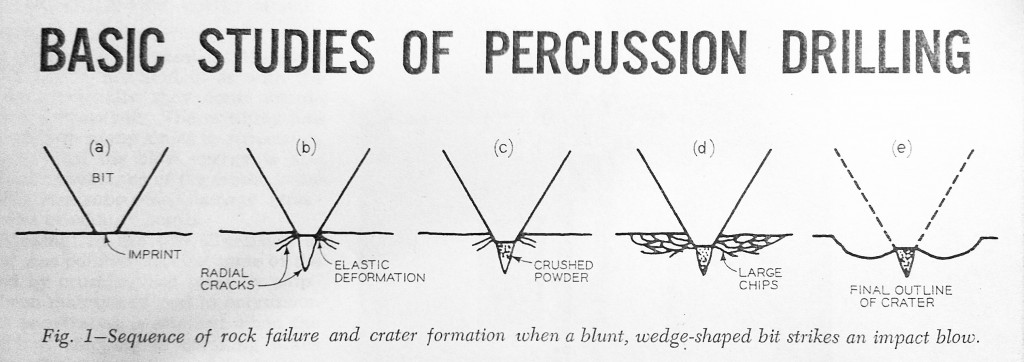
The tests were done on a flat surface rather than in a hole so they could photograph the process. In actual use, the bit is in a hole and the chipping might be limited by the space available at the base of the hole.
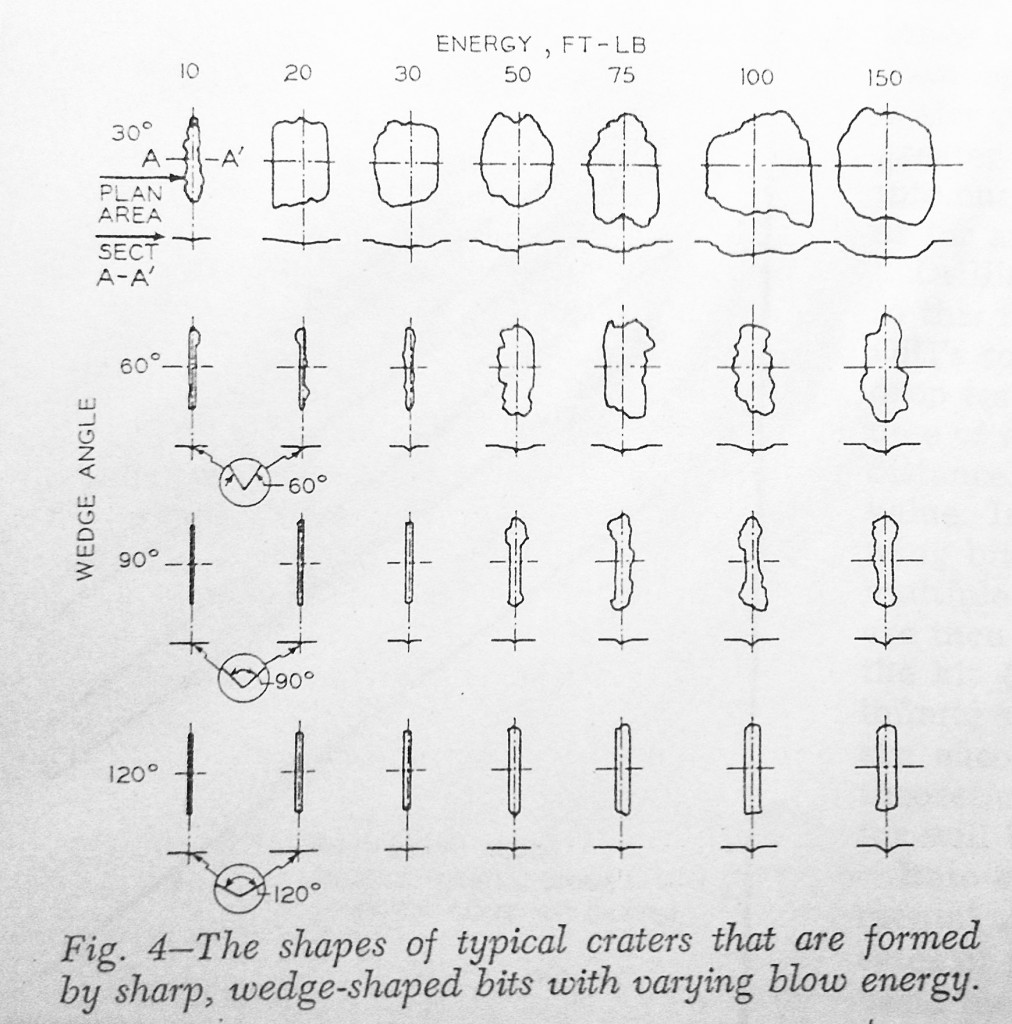
In Fig. 4 I think they used 1.5 inch drills which must be the standard for drilling blasting holes in mines.
The width and depth (or volume) of the crater is a function of the included angle of the tip, the sharpness of the bit, the blow energy and the rock. The rock factors might be the crushing strength, the shear strength and the grain size.
My conclusion is that part of the reason a 3/8 drill is faster than a 1/4 inch drill is because the larger hole size allows more chipping and less pulverization. This could be checked by collecting the crushed rock from a 3/8 inch hole and from a 1/4 inch hole then analyze the samples for particle size. Very boring work but I did this particle size analysis in soils lab as a student.
Indexing is what the author uses to describe the amount of rotation between each blow. He states that indexing can be too small and reduce drilling efficiency but cannot be to large. Maximum indexing is one half the angle between the cutting edges of the bit which is 90 degrees for the flat tip bits we use. If you use a cross tip, it would be 45 degrees. I really don't know what the minimum rotation is but for the single cutter bits we use but it must be 90 degrees or less. I generally rotate at least 15 degrees per blow. 30 degrees might be better but my wrist will only twist so much.
It may be that a 1/2 inch drill is faster than a 3/8 inch drill. Need to check that.
Unfortunately, the paper I have is only a summary of research. I'd like to see that original paper which was published by Drilling Research, Inc in "Collected Reports" vols 1-6 1949-1954. There is a copy of this at Stanford but I don't believe it can be checked out.
The 1954 vol 6 pp 9-18 seem to be what I want. If anybody is at Stanford, perhaps they could get me a photocopy or scan. Also 1953 2nd qtr pp 14-18.